BST-01 Ampoule Break Force Tester
- Standard: ISO 9187
- Manufacturer: Cell Instruments
- Applications: Packaging materials, medical device materials, pharmaceutical testing, and more.
- Customization: Available for special testing requirements and automation transformations
I. Introduction of the Glass Ampoule Break Force Tester
1. Definition and Primary Function
The Glass Ampoule Break Force Tester is an advanced instrument designed to measure the force required to break glass ampoules. This critical testing ensures the integrity and safety of pharmaceutical packaging, guaranteeing that ampoules can be opened with ease and consistency without compromising the contents.
2. Importance in the Industry
In the pharmaceutical and medical device industries, the quality and reliability of packaging are paramount. Glass ampoules are widely used for their impermeability and inertness, which protect the contents from contamination. The break force tester ensures that these ampoules meet strict safety and usability standards, thus preventing issues such as spillage, contamination, and user injury.
3. Key Benefits and Features
- Precision Testing: Accurate measurement of the force needed to break glass ampoules.
- Compliance with Standards: Ensures adherence to ISO 9187 requirements, providing confidence in the quality and safety of packaging.
- User-Friendly Interface: Easy operation with a touch screen interface.
- Safety Features: Includes protective covers and sample collection tubes to ensure safe testing procedures.
4. Applications
- Pharmaceutical Industry: Ensures the integrity and safety of drug packaging.
- Medical Device Manufacturing: Validates the quality of packaging materials used in medical devices.
- Quality Inspection Agencies: Provides reliable data for regulatory compliance and quality assurance.
- Research and Development: Assists in the development of new packaging solutions and materials.
II. Key Features and Specifications
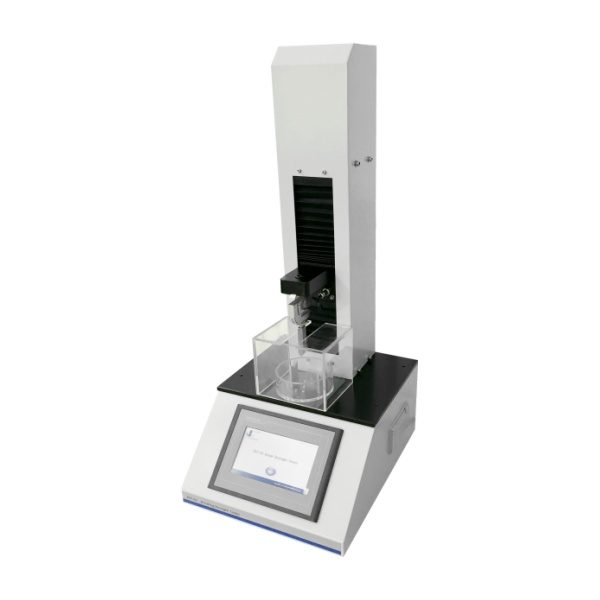
1. Technical Features
The Glass Ampoule Break Force Tester is equipped with advanced features that make it an essential tool in materials testing:
- PLC Control Unit: For precise and reliable control of the testing process.
- HMI Touch Screen: Simplifies user interaction and data input.
- Stepper Motor with Precision Ball-Lead Screw: Ensures accurate speed control and consistent testing conditions.
- Safety Features: Includes a sample collection tube for broken samples and a protective cover for errant pieces.
- Multiple Test Fixtures: Available in capacities of 1ml, 2ml, 5ml, 10ml, and 20ml, catering to various specifications.
- Versatile Testing: Supports testing of various materials used in medical packaging.
- Limiting Device and Automatic Return: Enhances operational safety and efficiency.
- Adjustable Test Speed: Customizable to meet different testing requirements.
- Dot Matrix Microprinter: Facilitates easy printing of test results.
- RS 232 Connectivity and Software: Optional features for enhanced data management and analysis.
2. Technical Specifications
Test Range | 0~200N (Or as required) |
Speed | 1~500mm/min |
Resolution | 0.1N |
Accuracy | 0.5% F.S. |
Power | 110~ 220V 50/60Hz |
III. Test Methods
1. Introduction to Test Methods
Consistent and accurate testing of glass ampoules is crucial for ensuring product safety and compliance. The break force test is a standardized method used to measure the force required to open glass ampoules, ensuring that they meet industry and regulatory standards.
2. Step-by-Step Testing Procedure
- Preparation of the Sample: Clean and inspect the ampoule to ensure it is free from defects.
- Setting Up the Tester: Install the appropriate test fixture and secure the ampoule in place.
- Executing the Break Force Test: Start the test using the touch screen interface. The machine applies force until the ampoule breaks.
- Recording and Analyzing Results: The tester records the break force, which can be printed or transferred to software for further analysis.
IV. ISO 9187 Standards
1. Overview of ISO 9187
ISO 9187 specifies the requirements and test methods for glass ampoules used in the pharmaceutical industry. It ensures that ampoules are easy to open, provide adequate protection for their contents, and are safe to handle.
2. Contents of ISO 9187
- Requirements for Glass Ampoules: Specifies dimensions, material properties, and manufacturing quality.
- Specifications for Break Force Testing: Details the methods for measuring the force required to open ampoules.
- Acceptable Limits and Criteria for Pass/Fail: Defines the acceptable range of break forces to ensure safety and usability.
3. Compliance with ISO 9187
- Ensuring Compliance: The Glass Ampoule Break Force Tester is designed to meet ISO 9187 standards, providing reliable and accurate testing results.
- Benefits of Adhering to ISO Standards: Ensures product safety, enhances consumer trust, and meets regulatory requirements.
- Case Studies or Examples of Compliance: Demonstrates real-world applications where adherence to ISO 9187 has ensured product quality and safety.
V. Customization
Special Testing Requirements
The Glass Ampoule Break Force Tester can be customized to meet specific testing needs. Customizable test parameters and setups ensure that unique requirements for various types of glass ampoules and packaging materials can be accurately tested.
VI. FAQ
The primary function is to measure the force required to break glass ampoules, ensuring they meet safety and usability standards.
The tester is designed to adhere to the specifications and requirements outlined in ISO 9187, ensuring consistent and reliable testing results.
It ensures the integrity and safety of pharmaceutical packaging, reduces the risk of contamination, and enhances compliance with regulatory standards.
Yes, it offers customizable test parameters and fixtures to accommodate various ampoule sizes and specifications.
Safety features include a protective cover for errant pieces, a sample collection tube for broken samples, and a limiting device for enhanced operational safety.