LT-03 Leak Tester
- Standard: ASTM D3078, ASTM D4991
- Manufacturer: Cell Instruments
- Applications: Packaging materials, medical device materials, pharmaceutical testing, adhesives, textiles, paper and cardboard containers, and more.
- Customization: Available for special testing requirements and automation transformations
I. Introduction of Bubble Leak Test Equipment
1. Definition and Purpose of the Equipment
Bubble Leak Test Equipment is a crucial instrument used to detect leaks in various packaging materials. This method identifies leaks by immersing the package in a liquid and applying a vacuum to observe if bubbles form, indicating a breach. The primary purpose of this equipment is to ensure the integrity and safety of packaged products, preventing contamination and preserving quality.
2. Importance in Various Industries
Bubble Leak Test Equipment is vital across multiple industries, including packaging, medical devices, and pharmaceuticals. In the packaging industry, it ensures that products are securely sealed, preventing spoilage and damage. In the medical and pharmaceutical sectors, it is critical to ensure that sterile packaging remains uncontaminated, safeguarding patient health.
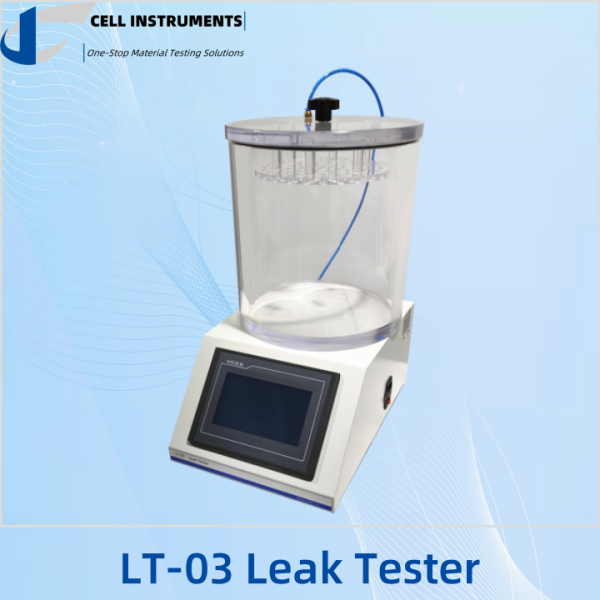
3. Key Features
- PLC-controlled unit (industrial-level stability) with HMI touch screen operation.
- To achieve a stable vacuum, considering the ease of obtaining compressed air, a Venturi tube is used for a vacuum level of up to -90KPa.
- This testing method relies on visual observation, providing cumulative result numbers instead of direct Pass/Fail outcomes.
- LT-03 offers a parameter-saving function for 5 groups, optimizing efficiency for users with diverse samples and test conditions (vacuum level and test time).
- Robust and transparent chamber with customization options for various sizes and shapes.
- Optional inclusion of a micro printer for sample identification.
- Optional adaptation for display in local languages.
- Modification capability to work with a vacuum pump, enabling higher vacuum.
II. Key Parameter
Test Range | 0~-90 KPa |
Chamber | Acrylic Cylinder Shape |
Test Space | Φ270*H210mm (Inside Usable) |
Compressed Air | 0.7MPa (Prepared by user) |
Power | 110~220V 50/60Hz |
III. Test Methods
1. Principle of Operation
The bubble leak test operates on a simple yet effective principle: immersing the test sample in a liquid and applying a vacuum. If the package has a leak, air will escape and form bubbles in the liquid, indicating a breach.
- Basic Steps:
- Immerse the package in a liquid bath.
- Apply a vacuum to the chamber.
- Observe for bubbles escaping from the package.
2. Procedure for Conducting the Test
- Preparation of the Sample:
- Ensure the sample is clean and free from any external contaminants.
- Seal the package as it would be in normal use.
- Setting Up the Equipment:
- Fill the chamber with the required liquid.
- Place the sample in the chamber and close it securely.
- Performing the Test:
- Apply the vacuum as per the equipment’s specifications.
- Monitor for bubbles forming around the sample.
- Recording and Interpreting Results:
- Note the presence and location of any bubbles.
- Determine the severity and potential impact of the leak.
IV. Relevant Standards
1. ASTM D3078
- Overview of the Standard: ASTM D3078 outlines the standard test method for detecting gross leaks in flexible packaging containing a headspace gas.
- Scope and Applications: This standard is used primarily for flexible packaging in the food and pharmaceutical industries.
- Detailed Description:
- Sample Preparation: Packages are prepared in a standard manner, ensuring they are filled with the appropriate product and sealed.
- Test Procedure: Involves immersing the package in a fluid and applying a vacuum to observe for bubble formation.
- Result Interpretation: Any bubble formation indicates a leak, and the location and size of the bubbles can help determine the severity of the leak.
2. ASTM D4991
- Overview of the Standard: ASTM D4991 specifies the test method for determining the leak tightness of package closures.
- Scope and Applications: Applicable to various types of packaging, including bottles, vials, and other rigid containers.
- Detailed Description:
- Sample Preparation: Packages are filled and sealed as per their intended use.
- Test Procedure: Similar to ASTM D3078, involves submerging the package and applying a vacuum.
- Result Interpretation: Observations of bubbles indicate leaks, and the test helps in assessing the integrity of the package closure.
V. Applications
- Packaging Industry: Ensures that products are securely sealed to prevent spoilage and damage during transportation and storage.
- Medical Devices: Verifies the integrity of sterile packaging to prevent contamination and ensure patient safety.
- Pharmaceuticals: Critical for maintaining the sterility and efficacy of medications by detecting leaks in their packaging.
VI. Customization Options
- Customizable Features and Configurations: Tailored to meet specific testing requirements and accommodate various package sizes and types.
- Special Testing Requirements: Can be adapted for unique testing conditions or specific industry needs.
VII. FAQ
Bubble Leak Test Equipment is used to detect leaks in packaging materials by observing for bubble formation when the package is submerged in a liquid and a vacuum is applied.
The method involves immersing the package in a liquid and applying a vacuum. If there is a leak, air will escape from the package, forming bubbles in the liquid.
ASTM D3078 focuses on detecting gross leaks in flexible packaging with headspace gas, while ASTM D4991 is for determining leak tightness in package closures for various rigid containers.
Yes, the equipment can be customized with various features and configurations to meet specific testing requirements and accommodate different package sizes and types.
Industries such as packaging, medical devices, and pharmaceuticals benefit significantly from using Bubble Leak Test Equipment to ensure the integrity and safety of their products.